Sound Tips
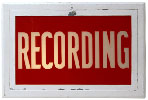
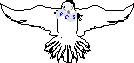
Phun City Sound "A Sound Choice in Sound Reinforcement and Engineering"
A Member of The Tasco Group
Microphones Part 1
Microphone applications: Why dynamic or condenser.
Most sound reinforcement applications like Church Sound, use primarily dynamic microphones for all applications. Primarily because of cost, secondly durability with a relatively high frequency response and third because of low feedback occurrence.
When the sound level and the quality of the reproduction grows, the condenser microphone becomes the mic of choice. The cost per microphone is increased, the high sound pressure level capability and frequency response extremely good. But the Sound control equipment and processing costs increase as well.
Here are some of the technical reasons behind the microphone.
A microphone is a pressure gradient transducer that converts acoustical energy into electrical energy. As pressure increases on the surface of the diaphragm, voltage is created. There are two main types of mic capsules. One is dynamic and the is condenser. A dynamic mic element consists of a fine coil of wire attached to a delicate diaphragm suspended in a permanent magnetic field. When sound waves strike the diaphragm, it vibrates with the frequency and the coil moves up and down in proportions to the wave intensity. This causes the coil to cut across the fixed lines of magnetic flux within the air gap of the permanent magnet. Because of this permanent magnetic field and the moving coil of wire suspended around it, a dynamic mic produces its own voltage. This process is electromagnetic.
With a condenser microphone, the capsule consists of two very thin plates. One plate is fixed (usually the back plate), and th3e other plate is movable. The movable plate is usually a thin, gold plated piece of plastic. These two plates form a capacitor. The capacitor is polarized by an external power supply. Positive pressure on the movable plate creates a positive voltage to be emitted from the capacitor. This process of a variable capacitor is electrostatic. Since these variable voltages are extremely minute, condenser mics need a preamplifier to boost the signal.. All condenser microphones have a small preamp built into the handle of the mic. This preamp is very sensitive and has the tendency to be fragile. The condenser element also tends to be effected by high humidity and temperature changes.
These disadvantages are outweighed by the accuracy and rapid response of the condenser. By not having a coil of wire and the large mass of a diaphragm, the condenser is superb when reproducing high frequency information, transients and overtones..
Most condenser microphones have an attenuator or pad located between the capsule and the preamp.. The pad keeps the preamp from overloading when extremely loud sound is entering the capsule/.
The preamplifier is powered by and external source. 'this dc voltage (commonly 9 to 48 volts) is usually called phantom power, and is provided by the console. In most condenser microphones, the phantom power source also provides the static charge for the element.
There has been a lot of confusion of terminology when describing condenser microphones. Terms like condenser, true condenser, air condenser, electret, and electret condenser have been used.
The electret diaphragm is made of a special plastic that retains an indefinite static charge. The manufacturer charges the diaphragm with an electron beam. Even though the condenser element doesn't need an external voltage to charge it, the electret condenser mic still needs a voltage source to operate the internal preamp. This is why most electret microphones have a battery installed in the handle.
Regardless of the type of condenser, the transducer is a variable capacitor and differs only in the method by which the capacitor is biases. The performance of the condenser microphone should not be influenced by the method of how it gets its bias voltage. As a matter of fact, some electret condenser microphones use phantom power and have an internal battery as a backup power supply if the phantom voltage fails.
The earliest of all microphones is the carbon element. A small bowl is filled with powdered carbon and enclosed at one end with a brass button. This button is connected to a metal diaphragm. The button and the rear of the carbon filled cup are connected to a voltage source that activates the carbon particles. Then sound hits the diaphragm, the carbon powder is caused to vibrate becoming more and less dense as the button moves. The electrical resistance of the fluctuating carbon is converted into and electrical representation of the sound wave. The output voltage of the capsule is fed into a step-up transformer and proceeds to the amplifier.
Carbon microphones are not used in the recording studio because they don't have a very good frequency response curve and carbon granules can become clotted and produce little or no output. They are still used today in a lo9t of utility applications such as telephone handsets and handset intercoms.
Another early microphone is the crystal mic. The crystal microphone works on a piezoelectric (pressure-electrical) principle. A small pin is attached to a diaphragm and rests against a thin crystal. When a sound strikes the diaphragm, and it vibrates, the created pressure bends the crystal. This bending creates voltage and the voltage is a representation of the associated sound.
Crystal microphones are very cheap to make and exhibit high output voltages. This makes them popular in the manufacture of children's audio toys and piezo-electric contact pickups. But for recording purposes, they are too fragile and have a rather poor frequency response curve.
|